ਇਹ ਚੰਗੀ ਤਰ੍ਹਾਂ ਜਾਣਿਆ ਜਾਂਦਾ ਹੈ ਕਿ ਸਰਕਟ ਬੋਰਡਾਂ ਦੀ ਸਭ ਤੋਂ ਵਧੀਆ ਵਿਸ਼ੇਸ਼ਤਾ ਸੀਮਤ ਥਾਂਵਾਂ ਵਿੱਚ ਗੁੰਝਲਦਾਰ ਸਰਕਟ ਲੇਆਉਟ ਦੀ ਆਗਿਆ ਦੇਣਾ ਹੈ। ਹਾਲਾਂਕਿ, ਜਦੋਂ ਇਹ OEM PCBA (ਮੂਲ ਉਪਕਰਣ ਨਿਰਮਾਤਾ ਪ੍ਰਿੰਟਿਡ ਸਰਕਟ ਬੋਰਡ ਅਸੈਂਬਲੀ) ਡਿਜ਼ਾਈਨ ਦੀ ਗੱਲ ਆਉਂਦੀ ਹੈ, ਖਾਸ ਤੌਰ 'ਤੇ ਨਿਯੰਤਰਿਤ ਰੁਕਾਵਟ, ਇੰਜੀਨੀਅਰਾਂ ਨੂੰ ਕਈ ਸੀਮਾਵਾਂ ਅਤੇ ਚੁਣੌਤੀਆਂ ਨੂੰ ਪਾਰ ਕਰਨਾ ਪੈਂਦਾ ਹੈ। ਅੱਗੇ, ਇਹ ਲੇਖ ਇੱਕ ਨਿਯੰਤਰਿਤ ਰੁਕਾਵਟ ਦੇ ਨਾਲ ਇੱਕ ਸਖ਼ਤ-ਫਲੈਕਸ ਪੀਸੀਬੀ ਨੂੰ ਡਿਜ਼ਾਈਨ ਕਰਨ ਦੀਆਂ ਸੀਮਾਵਾਂ ਨੂੰ ਪ੍ਰਗਟ ਕਰੇਗਾ।
ਸਖ਼ਤ-ਫਲੈਕਸ ਪੀਸੀਬੀ ਡਿਜ਼ਾਈਨ
Rigid-Flex PCBs ਸਖ਼ਤ ਅਤੇ ਲਚਕੀਲੇ ਸਰਕਟ ਬੋਰਡਾਂ ਦਾ ਇੱਕ ਹਾਈਬ੍ਰਿਡ ਹਨ, ਦੋਵੇਂ ਤਕਨਾਲੋਜੀਆਂ ਨੂੰ ਇੱਕ ਇਕਾਈ ਵਿੱਚ ਜੋੜਦੇ ਹੋਏ। ਇਹ ਡਿਜ਼ਾਇਨ ਪਹੁੰਚ ਉਹਨਾਂ ਐਪਲੀਕੇਸ਼ਨਾਂ ਵਿੱਚ ਵਧੇਰੇ ਲਚਕਤਾ ਦੀ ਆਗਿਆ ਦਿੰਦੀ ਹੈ ਜਿੱਥੇ ਸਪੇਸ ਪ੍ਰੀਮੀਅਮ 'ਤੇ ਹੈ, ਜਿਵੇਂ ਕਿ ਮੈਡੀਕਲ ਡਿਵਾਈਸਾਂ, ਏਰੋਸਪੇਸ, ਅਤੇ ਖਪਤਕਾਰ ਇਲੈਕਟ੍ਰੋਨਿਕਸ ਵਿੱਚ। ਇਸਦੀ ਅਖੰਡਤਾ ਨਾਲ ਸਮਝੌਤਾ ਕੀਤੇ ਬਿਨਾਂ ਪੀਸੀਬੀ ਨੂੰ ਮੋੜਨ ਅਤੇ ਫੋਲਡ ਕਰਨ ਦੀ ਯੋਗਤਾ ਇੱਕ ਮਹੱਤਵਪੂਰਨ ਫਾਇਦਾ ਹੈ। ਹਾਲਾਂਕਿ, ਇਹ ਲਚਕਤਾ ਚੁਣੌਤੀਆਂ ਦੇ ਆਪਣੇ ਸਮੂਹ ਦੇ ਨਾਲ ਆਉਂਦੀ ਹੈ, ਖਾਸ ਤੌਰ 'ਤੇ ਜਦੋਂ ਇਹ ਰੁਕਾਵਟ ਨਿਯੰਤਰਣ ਦੀ ਗੱਲ ਆਉਂਦੀ ਹੈ।
ਸਖ਼ਤ-ਫਲੈਕਸ ਪੀਸੀਬੀਜ਼ ਦੀਆਂ ਰੁਕਾਵਟਾਂ ਦੀਆਂ ਲੋੜਾਂ
ਹਾਈ-ਸਪੀਡ ਡਿਜੀਟਲ ਅਤੇ RF (ਰੇਡੀਓ ਫ੍ਰੀਕੁਐਂਸੀ) ਐਪਲੀਕੇਸ਼ਨਾਂ ਵਿੱਚ ਅੜਿੱਕਾ ਨਿਯੰਤਰਣ ਮਹੱਤਵਪੂਰਨ ਹੈ। ਪੀਸੀਬੀ ਦੀ ਰੁਕਾਵਟ ਸਿਗਨਲ ਦੀ ਇਕਸਾਰਤਾ ਨੂੰ ਪ੍ਰਭਾਵਤ ਕਰਦੀ ਹੈ, ਜਿਸ ਨਾਲ ਸਿਗਨਲ ਦਾ ਨੁਕਸਾਨ, ਪ੍ਰਤੀਬਿੰਬ ਅਤੇ ਕ੍ਰਾਸਸਟਾਲ ਵਰਗੀਆਂ ਸਮੱਸਿਆਵਾਂ ਪੈਦਾ ਹੋ ਸਕਦੀਆਂ ਹਨ। ਸਖ਼ਤ-ਫਲੈਕਸ PCBs ਲਈ, ਸਰਵੋਤਮ ਪ੍ਰਦਰਸ਼ਨ ਨੂੰ ਯਕੀਨੀ ਬਣਾਉਣ ਲਈ ਪੂਰੇ ਡਿਜ਼ਾਈਨ ਦੌਰਾਨ ਇਕਸਾਰ ਰੁਕਾਵਟ ਨੂੰ ਕਾਇਮ ਰੱਖਣਾ ਜ਼ਰੂਰੀ ਹੈ।
ਆਮ ਤੌਰ 'ਤੇ, ਸਖ਼ਤ-ਫਲੈਕਸ PCBs ਲਈ ਅੜਿੱਕਾ ਰੇਂਜ ਐਪਲੀਕੇਸ਼ਨ 'ਤੇ ਨਿਰਭਰ ਕਰਦੇ ਹੋਏ, 50 ohms ਅਤੇ 75 ohms ਵਿਚਕਾਰ ਨਿਰਧਾਰਤ ਕੀਤੀ ਜਾਂਦੀ ਹੈ। ਹਾਲਾਂਕਿ, ਇਸ ਨਿਯੰਤਰਿਤ ਰੁਕਾਵਟ ਨੂੰ ਪ੍ਰਾਪਤ ਕਰਨਾ ਸਖ਼ਤ-ਫਲੈਕਸ ਡਿਜ਼ਾਈਨ ਦੀਆਂ ਵਿਲੱਖਣ ਵਿਸ਼ੇਸ਼ਤਾਵਾਂ ਦੇ ਕਾਰਨ ਚੁਣੌਤੀਪੂਰਨ ਹੋ ਸਕਦਾ ਹੈ। ਵਰਤੀਆਂ ਗਈਆਂ ਸਮੱਗਰੀਆਂ, ਪਰਤਾਂ ਦੀ ਮੋਟਾਈ, ਅਤੇ ਡਾਈਇਲੈਕਟ੍ਰਿਕ ਵਿਸ਼ੇਸ਼ਤਾਵਾਂ ਸਾਰੇ ਰੁਕਾਵਟ ਨੂੰ ਨਿਰਧਾਰਤ ਕਰਨ ਵਿੱਚ ਮਹੱਤਵਪੂਰਨ ਭੂਮਿਕਾ ਨਿਭਾਉਂਦੇ ਹਨ।
ਸਖ਼ਤ-ਫਲੈਕਸ ਪੀਸੀਬੀ ਸਟੈਕ-ਅੱਪ ਦੀਆਂ ਸੀਮਾਵਾਂ
ਨਿਯੰਤਰਿਤ ਰੁਕਾਵਟ ਦੇ ਨਾਲ ਸਖ਼ਤ-ਫਲੈਕਸ PCBs ਨੂੰ ਡਿਜ਼ਾਈਨ ਕਰਨ ਵਿੱਚ ਪ੍ਰਾਇਮਰੀ ਸੀਮਾਵਾਂ ਵਿੱਚੋਂ ਇੱਕ ਸਟੈਕ-ਅੱਪ ਸੰਰਚਨਾ ਹੈ। ਸਟੈਕ-ਅੱਪ ਪੀਸੀਬੀ ਵਿੱਚ ਪਰਤਾਂ ਦੇ ਪ੍ਰਬੰਧ ਨੂੰ ਦਰਸਾਉਂਦਾ ਹੈ, ਜਿਸ ਵਿੱਚ ਤਾਂਬੇ ਦੀਆਂ ਪਰਤਾਂ, ਡਾਈਇਲੈਕਟ੍ਰਿਕ ਸਮੱਗਰੀ, ਅਤੇ ਚਿਪਕਣ ਵਾਲੀਆਂ ਪਰਤਾਂ ਸ਼ਾਮਲ ਹੋ ਸਕਦੀਆਂ ਹਨ। ਸਖ਼ਤ-ਫਲੈਕਸ ਡਿਜ਼ਾਈਨਾਂ ਵਿੱਚ, ਸਟੈਕ-ਅਪ ਵਿੱਚ ਸਖ਼ਤ ਅਤੇ ਲਚਕੀਲੇ ਭਾਗਾਂ ਨੂੰ ਸ਼ਾਮਲ ਕਰਨਾ ਚਾਹੀਦਾ ਹੈ, ਜੋ ਰੁਕਾਵਟ ਨਿਯੰਤਰਣ ਪ੍ਰਕਿਰਿਆ ਨੂੰ ਗੁੰਝਲਦਾਰ ਬਣਾ ਸਕਦੇ ਹਨ।
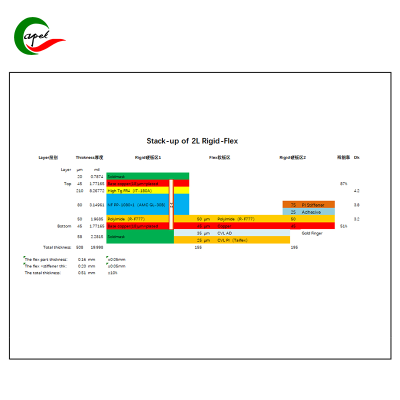
1. ਪਦਾਰਥਕ ਪਾਬੰਦੀਆਂ
ਸਖ਼ਤ-ਫਲੈਕਸ PCBs ਵਿੱਚ ਵਰਤੀਆਂ ਜਾਣ ਵਾਲੀਆਂ ਸਮੱਗਰੀਆਂ ਰੁਕਾਵਟਾਂ ਨੂੰ ਮਹੱਤਵਪੂਰਨ ਤੌਰ 'ਤੇ ਪ੍ਰਭਾਵਤ ਕਰ ਸਕਦੀਆਂ ਹਨ। ਲਚਕੀਲੇ ਪਦਾਰਥਾਂ ਵਿੱਚ ਕਠੋਰ ਸਮੱਗਰੀਆਂ ਦੀ ਤੁਲਨਾ ਵਿੱਚ ਅਕਸਰ ਵੱਖ-ਵੱਖ ਡਾਈਇਲੈਕਟ੍ਰਿਕ ਸਥਿਰਾਂਕ ਹੁੰਦੇ ਹਨ। ਇਹ ਅੰਤਰ ਰੁਕਾਵਟ ਵਿੱਚ ਭਿੰਨਤਾਵਾਂ ਪੈਦਾ ਕਰ ਸਕਦਾ ਹੈ ਜਿਨ੍ਹਾਂ ਨੂੰ ਨਿਯੰਤਰਿਤ ਕਰਨਾ ਮੁਸ਼ਕਲ ਹੈ। ਇਸ ਤੋਂ ਇਲਾਵਾ, ਸਮੱਗਰੀ ਦੀ ਚੋਣ ਪੀਸੀਬੀ ਦੀ ਸਮੁੱਚੀ ਕਾਰਗੁਜ਼ਾਰੀ ਨੂੰ ਪ੍ਰਭਾਵਿਤ ਕਰ ਸਕਦੀ ਹੈ, ਜਿਸ ਵਿੱਚ ਥਰਮਲ ਸਥਿਰਤਾ ਅਤੇ ਮਕੈਨੀਕਲ ਤਾਕਤ ਸ਼ਾਮਲ ਹੈ।
2. ਲੇਅਰ ਮੋਟਾਈ ਪਰਿਵਰਤਨਸ਼ੀਲਤਾ
ਇੱਕ ਕਠੋਰ-ਫਲੈਕਸ ਪੀਸੀਬੀ ਵਿੱਚ ਲੇਅਰਾਂ ਦੀ ਮੋਟਾਈ ਸਖ਼ਤ ਅਤੇ ਲਚਕੀਲੇ ਭਾਗਾਂ ਵਿੱਚ ਮਹੱਤਵਪੂਰਨ ਤੌਰ 'ਤੇ ਵੱਖ-ਵੱਖ ਹੋ ਸਕਦੀ ਹੈ। ਇਹ ਪਰਿਵਰਤਨਸ਼ੀਲਤਾ ਪੂਰੇ ਬੋਰਡ ਵਿਚ ਇਕਸਾਰ ਰੁਕਾਵਟ ਨੂੰ ਕਾਇਮ ਰੱਖਣ ਵਿਚ ਚੁਣੌਤੀਆਂ ਪੈਦਾ ਕਰ ਸਕਦੀ ਹੈ। ਇੰਜੀਨੀਅਰਾਂ ਨੂੰ ਇਹ ਯਕੀਨੀ ਬਣਾਉਣ ਲਈ ਹਰੇਕ ਪਰਤ ਦੀ ਮੋਟਾਈ ਦੀ ਧਿਆਨ ਨਾਲ ਗਣਨਾ ਕਰਨੀ ਚਾਹੀਦੀ ਹੈ ਕਿ ਰੁਕਾਵਟ ਨਿਰਧਾਰਤ ਸੀਮਾ ਦੇ ਅੰਦਰ ਹੀ ਰਹੇ।
3. ਰੇਡੀਅਸ ਵਿਚਾਰਾਂ ਨੂੰ ਮੋੜੋ
ਇੱਕ ਸਖ਼ਤ-ਫਲੈਕਸ ਪੀਸੀਬੀ ਦਾ ਮੋੜ ਦਾ ਘੇਰਾ ਇੱਕ ਹੋਰ ਮਹੱਤਵਪੂਰਨ ਕਾਰਕ ਹੈ ਜੋ ਰੁਕਾਵਟ ਨੂੰ ਪ੍ਰਭਾਵਿਤ ਕਰ ਸਕਦਾ ਹੈ। ਜਦੋਂ ਪੀਸੀਬੀ ਮੋੜਿਆ ਜਾਂਦਾ ਹੈ, ਤਾਂ ਡਾਈਇਲੈਕਟ੍ਰਿਕ ਸਮੱਗਰੀ ਸੰਕੁਚਿਤ ਜਾਂ ਖਿੱਚ ਸਕਦੀ ਹੈ, ਰੁਕਾਵਟ ਦੀਆਂ ਵਿਸ਼ੇਸ਼ਤਾਵਾਂ ਨੂੰ ਬਦਲ ਸਕਦੀ ਹੈ। ਡਿਜ਼ਾਈਨਰਾਂ ਨੂੰ ਇਹ ਯਕੀਨੀ ਬਣਾਉਣ ਲਈ ਕਿ ਓਪਰੇਸ਼ਨ ਦੌਰਾਨ ਰੁਕਾਵਟ ਸਥਿਰ ਰਹਿੰਦੀ ਹੈ, ਉਹਨਾਂ ਦੀਆਂ ਗਣਨਾਵਾਂ ਵਿੱਚ ਮੋੜ ਦੇ ਘੇਰੇ ਦਾ ਲੇਖਾ-ਜੋਖਾ ਕਰਨਾ ਚਾਹੀਦਾ ਹੈ।
4. ਨਿਰਮਾਣ ਸਹਿਣਸ਼ੀਲਤਾ
ਮੈਨੂਫੈਕਚਰਿੰਗ ਸਹਿਣਸ਼ੀਲਤਾ ਵੀ ਸਖ਼ਤ-ਫਲੈਕਸ ਪੀਸੀਬੀ ਵਿੱਚ ਨਿਯੰਤਰਿਤ ਰੁਕਾਵਟ ਨੂੰ ਪ੍ਰਾਪਤ ਕਰਨ ਵਿੱਚ ਚੁਣੌਤੀਆਂ ਪੈਦਾ ਕਰ ਸਕਦੀ ਹੈ। ਨਿਰਮਾਣ ਪ੍ਰਕਿਰਿਆ ਵਿੱਚ ਭਿੰਨਤਾਵਾਂ ਪਰਤ ਦੀ ਮੋਟਾਈ, ਪਦਾਰਥਕ ਵਿਸ਼ੇਸ਼ਤਾਵਾਂ ਅਤੇ ਸਮੁੱਚੇ ਮਾਪਾਂ ਵਿੱਚ ਅਸੰਗਤਤਾਵਾਂ ਦਾ ਕਾਰਨ ਬਣ ਸਕਦੀਆਂ ਹਨ। ਇਹ ਅਸੰਗਤਤਾਵਾਂ ਦੇ ਨਤੀਜੇ ਵਜੋਂ ਅੜਿੱਕਾ ਬੇਮੇਲ ਹੋ ਸਕਦਾ ਹੈ ਜੋ ਸਿਗਨਲ ਦੀ ਇਕਸਾਰਤਾ ਨੂੰ ਘਟਾ ਸਕਦਾ ਹੈ।
5. ਜਾਂਚ ਅਤੇ ਪ੍ਰਮਾਣਿਕਤਾ
ਨਿਯੰਤਰਿਤ ਰੁਕਾਵਟ ਲਈ ਸਖ਼ਤ-ਫਲੈਕਸ PCBs ਦੀ ਜਾਂਚ ਰਵਾਇਤੀ ਸਖ਼ਤ ਜਾਂ ਲਚਕਦਾਰ PCBs ਨਾਲੋਂ ਵਧੇਰੇ ਗੁੰਝਲਦਾਰ ਹੋ ਸਕਦੀ ਹੈ। ਬੋਰਡ ਦੇ ਵੱਖ-ਵੱਖ ਭਾਗਾਂ ਵਿੱਚ ਰੁਕਾਵਟ ਨੂੰ ਸਹੀ ਢੰਗ ਨਾਲ ਮਾਪਣ ਲਈ ਵਿਸ਼ੇਸ਼ ਸਾਜ਼ੋ-ਸਾਮਾਨ ਅਤੇ ਤਕਨੀਕਾਂ ਦੀ ਲੋੜ ਹੋ ਸਕਦੀ ਹੈ। ਇਹ ਜੋੜੀ ਗਈ ਗੁੰਝਲਤਾ ਡਿਜ਼ਾਈਨ ਅਤੇ ਨਿਰਮਾਣ ਪ੍ਰਕਿਰਿਆ ਨਾਲ ਜੁੜੇ ਸਮੇਂ ਅਤੇ ਲਾਗਤ ਨੂੰ ਵਧਾ ਸਕਦੀ ਹੈ।
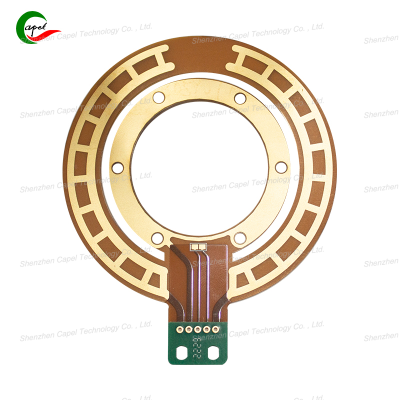
ਪੋਸਟ ਟਾਈਮ: ਅਕਤੂਬਰ-28-2024
ਪਿੱਛੇ