ਇਲੈਕਟ੍ਰੋਨਿਕਸ ਦੀ ਦੁਨੀਆ ਵਿੱਚ, ਉੱਚ-ਪ੍ਰਦਰਸ਼ਨ ਵਾਲੇ ਪ੍ਰਿੰਟਿਡ ਸਰਕਟ ਬੋਰਡਾਂ (ਪੀਸੀਬੀ) ਦੀ ਮੰਗ ਨੇ ਸਖ਼ਤ-ਫਲੈਕਸ ਪੀਸੀਬੀ ਡਿਜ਼ਾਈਨ ਦੇ ਵਿਕਾਸ ਵੱਲ ਅਗਵਾਈ ਕੀਤੀ ਹੈ। ਇਹ ਨਵੀਨਤਾਕਾਰੀ ਬੋਰਡ ਸਖ਼ਤ ਅਤੇ ਲਚਕਦਾਰ PCBs ਦੀਆਂ ਸਭ ਤੋਂ ਵਧੀਆ ਵਿਸ਼ੇਸ਼ਤਾਵਾਂ ਨੂੰ ਜੋੜਦੇ ਹਨ, ਸਪੇਸ-ਬਚਤ, ਭਾਰ ਘਟਾਉਣ ਅਤੇ ਵਧੀ ਹੋਈ ਭਰੋਸੇਯੋਗਤਾ ਦੇ ਰੂਪ ਵਿੱਚ ਵਿਲੱਖਣ ਫਾਇਦੇ ਪੇਸ਼ ਕਰਦੇ ਹਨ। ਹਾਲਾਂਕਿ, ਇੱਕ ਨਾਜ਼ੁਕ ਪਹਿਲੂ ਜੋ ਅਕਸਰ ਡਿਜ਼ਾਈਨ ਪ੍ਰਕਿਰਿਆ ਵਿੱਚ ਨਜ਼ਰਅੰਦਾਜ਼ ਕੀਤਾ ਜਾਂਦਾ ਹੈ ਉਹ ਹੈ ਸਹੀ ਸੋਲਡਰਮਾਸਕ ਦੀ ਚੋਣ। ਇਹ ਲੇਖ ਖੋਜ ਕਰੇਗਾ ਕਿ ਰਿਜਿਡ-ਫਲੈਕਸ ਪੀਸੀਬੀ ਡਿਜ਼ਾਈਨ ਲਈ ਢੁਕਵੇਂ ਸੋਲਡਰਮਾਸਕ ਨੂੰ ਕਿਵੇਂ ਚੁਣਨਾ ਹੈ, ਪਦਾਰਥਕ ਵਿਸ਼ੇਸ਼ਤਾਵਾਂ, ਪੀਸੀਬੀ ਨਿਰਮਾਣ ਪ੍ਰਕਿਰਿਆ ਨਾਲ ਅਨੁਕੂਲਤਾ, ਅਤੇ ਸਖ਼ਤ-ਫਲੈਕਸ ਪੀਸੀਬੀ ਦੀਆਂ ਵਿਸ਼ੇਸ਼ ਸਮਰੱਥਾਵਾਂ ਵਰਗੇ ਕਾਰਕਾਂ ਨੂੰ ਧਿਆਨ ਵਿੱਚ ਰੱਖਦੇ ਹੋਏ।
ਸਖ਼ਤ-ਫਲੈਕਸ ਪੀਸੀਬੀ ਡਿਜ਼ਾਈਨ ਨੂੰ ਜਾਣਨਾ
Rigid-Flex PCBs ਸਖ਼ਤ ਅਤੇ ਲਚਕਦਾਰ ਸਰਕਟ ਤਕਨੀਕਾਂ ਦਾ ਇੱਕ ਹਾਈਬ੍ਰਿਡ ਹਨ, ਜੋ ਗੁੰਝਲਦਾਰ ਡਿਜ਼ਾਈਨਾਂ ਦੀ ਇਜਾਜ਼ਤ ਦਿੰਦੇ ਹਨ ਜੋ ਪ੍ਰਦਰਸ਼ਨ ਨਾਲ ਸਮਝੌਤਾ ਕੀਤੇ ਬਿਨਾਂ ਮੋੜ ਅਤੇ ਫਲੈਕਸ ਕਰ ਸਕਦੇ ਹਨ। Rigid-Flex PCBs ਵਿੱਚ ਲੇਅਰ ਸਟੈਕਅਪ ਵਿੱਚ ਆਮ ਤੌਰ 'ਤੇ ਸਖ਼ਤ ਅਤੇ ਲਚਕਦਾਰ ਸਮੱਗਰੀਆਂ ਦੀਆਂ ਕਈ ਪਰਤਾਂ ਹੁੰਦੀਆਂ ਹਨ, ਜੋ ਖਾਸ ਐਪਲੀਕੇਸ਼ਨ ਲੋੜਾਂ ਨੂੰ ਪੂਰਾ ਕਰਨ ਲਈ ਤਿਆਰ ਕੀਤੀਆਂ ਜਾ ਸਕਦੀਆਂ ਹਨ। ਇਹ ਬਹੁਪੱਖੀਤਾ ਏਰੋਸਪੇਸ, ਮੈਡੀਕਲ ਡਿਵਾਈਸਾਂ, ਅਤੇ ਉਪਭੋਗਤਾ ਇਲੈਕਟ੍ਰੋਨਿਕਸ ਵਿੱਚ ਐਪਲੀਕੇਸ਼ਨਾਂ ਲਈ ਸਖ਼ਤ-ਫਲੈਕਸ ਪੀਸੀਬੀ ਨੂੰ ਆਦਰਸ਼ ਬਣਾਉਂਦੀ ਹੈ, ਜਿੱਥੇ ਸਪੇਸ ਅਤੇ ਭਾਰ ਮਹੱਤਵਪੂਰਨ ਕਾਰਕ ਹਨ।
ਸਖ਼ਤ-ਫਲੈਕਸ ਪੀਸੀਬੀ ਡਿਜ਼ਾਈਨ ਵਿੱਚ ਸੋਲਡਰਮਾਸਕ ਦੀ ਭੂਮਿਕਾ
ਸੋਲਡਰਮਾਸਕ ਇੱਕ ਸੁਰੱਖਿਆ ਪਰਤ ਹੈ ਜੋ ਪੀਸੀਬੀ ਦੀ ਸਤ੍ਹਾ 'ਤੇ ਸੋਲਡਰ ਬ੍ਰਿਜਿੰਗ ਨੂੰ ਰੋਕਣ, ਵਾਤਾਵਰਣ ਦੇ ਨੁਕਸਾਨ ਤੋਂ ਬਚਾਉਣ ਅਤੇ ਬੋਰਡ ਦੀ ਸਮੁੱਚੀ ਟਿਕਾਊਤਾ ਨੂੰ ਵਧਾਉਣ ਲਈ ਲਗਾਈ ਜਾਂਦੀ ਹੈ। ਸਖ਼ਤ-ਫਲੈਕਸ ਪੀਸੀਬੀ ਡਿਜ਼ਾਈਨਾਂ ਵਿੱਚ, ਸੋਲਡਰਮਾਸਕ ਨੂੰ ਸਖ਼ਤ ਅਤੇ ਲਚਕੀਲੇ ਭਾਗਾਂ ਦੀਆਂ ਵਿਲੱਖਣ ਵਿਸ਼ੇਸ਼ਤਾਵਾਂ ਨੂੰ ਅਨੁਕੂਲਿਤ ਕਰਨਾ ਚਾਹੀਦਾ ਹੈ। ਇਹ ਉਹ ਥਾਂ ਹੈ ਜਿੱਥੇ ਸੋਲਡਰਮਾਸਕ ਸਮੱਗਰੀ ਦੀ ਚੋਣ ਮਹੱਤਵਪੂਰਨ ਬਣ ਜਾਂਦੀ ਹੈ.
ਵਿਚਾਰਨ ਲਈ ਸਮੱਗਰੀ ਦੀਆਂ ਵਿਸ਼ੇਸ਼ਤਾਵਾਂ
ਸਖ਼ਤ-ਫਲੈਕਸ ਪੀਸੀਬੀ ਲਈ ਸੋਲਡਰਮਾਸਕ ਦੀ ਚੋਣ ਕਰਦੇ ਸਮੇਂ, ਇਹ ਜ਼ਰੂਰੀ ਹੈ ਕਿ ਉਹ ਸਮੱਗਰੀ ਚੁਣੋ ਜੋ ਮਕੈਨੀਕਲ ਡਿਫੈਕਸ਼ਨ ਅਤੇ ਵਾਤਾਵਰਨ ਤਣਾਅ ਦਾ ਸਾਮ੍ਹਣਾ ਕਰ ਸਕੇ। ਹੇਠ ਲਿਖੀਆਂ ਵਿਸ਼ੇਸ਼ਤਾਵਾਂ 'ਤੇ ਵਿਚਾਰ ਕੀਤਾ ਜਾਣਾ ਚਾਹੀਦਾ ਹੈ:
ਵਿਘਨ ਪ੍ਰਤੀਰੋਧ:ਸੋਲਡਰਮਾਸਕ ਪੀਸੀਬੀ ਦੇ ਲਚਕੀਲੇ ਭਾਗਾਂ ਵਿੱਚ ਵਾਪਰਨ ਵਾਲੇ ਝੁਕਣ ਅਤੇ ਲਚਕੀਲੇਪਣ ਨੂੰ ਸਹਿਣ ਦੇ ਯੋਗ ਹੋਣਾ ਚਾਹੀਦਾ ਹੈ। ਸਕਰੀਨ ਪ੍ਰਿੰਟਿੰਗ ਲਚਕਦਾਰ ਤਰਲ ਫੋਟੋਸੈਂਸਟਿਵ ਡਿਵੈਲਪਮੈਂਟ ਸੋਲਡਰਮਾਸਕ ਸਿਆਹੀ ਇੱਕ ਸ਼ਾਨਦਾਰ ਵਿਕਲਪ ਹੈ, ਕਿਉਂਕਿ ਇਹ ਮਕੈਨੀਕਲ ਤਣਾਅ ਦੇ ਅਧੀਨ ਇਸਦੀ ਅਖੰਡਤਾ ਨੂੰ ਬਣਾਈ ਰੱਖਣ ਲਈ ਤਿਆਰ ਕੀਤਾ ਗਿਆ ਹੈ।
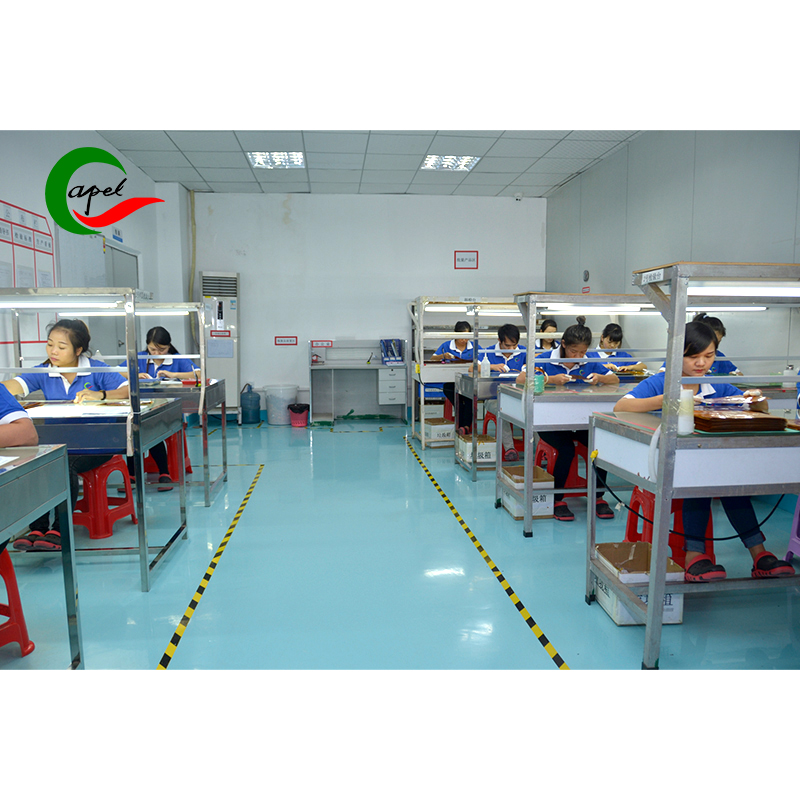
ਵੈਲਡਿੰਗ ਪ੍ਰਤੀਰੋਧ:ਸੋਲਡਰਮਾਸਕ ਨੂੰ ਅਸੈਂਬਲੀ ਪ੍ਰਕਿਰਿਆ ਦੌਰਾਨ ਸੋਲਡਰ ਦੇ ਵਿਰੁੱਧ ਇੱਕ ਮਜ਼ਬੂਤ ਰੁਕਾਵਟ ਪ੍ਰਦਾਨ ਕਰਨੀ ਚਾਹੀਦੀ ਹੈ। ਇਹ ਸੁਨਿਸ਼ਚਿਤ ਕਰਦਾ ਹੈ ਕਿ ਸੋਲਡਰ ਉਹਨਾਂ ਖੇਤਰਾਂ ਵਿੱਚ ਨਹੀਂ ਫਸਦਾ ਜਿੱਥੇ ਇਹ ਸ਼ਾਰਟ ਸਰਕਟ ਜਾਂ ਹੋਰ ਸਮੱਸਿਆਵਾਂ ਦਾ ਕਾਰਨ ਬਣ ਸਕਦਾ ਹੈ।
ਨਮੀ ਪ੍ਰਤੀਰੋਧ:ਇਹ ਧਿਆਨ ਵਿੱਚ ਰੱਖਦੇ ਹੋਏ ਕਿ ਸਖ਼ਤ-ਫਲੈਕਸ PCBs ਅਕਸਰ ਅਜਿਹੇ ਵਾਤਾਵਰਣ ਵਿੱਚ ਵਰਤੇ ਜਾਂਦੇ ਹਨ ਜਿੱਥੇ ਨਮੀ ਦਾ ਸਾਹਮਣਾ ਕਰਨਾ ਇੱਕ ਚਿੰਤਾ ਦਾ ਵਿਸ਼ਾ ਹੈ, ਸੋਲਡਰਮਾਸਕ ਨੂੰ ਅੰਡਰਲਾਈੰਗ ਸਰਕਟਰੀ ਦੇ ਖੋਰ ਅਤੇ ਪਤਨ ਨੂੰ ਰੋਕਣ ਲਈ ਵਧੀਆ ਨਮੀ ਪ੍ਰਤੀਰੋਧ ਦੀ ਪੇਸ਼ਕਸ਼ ਕਰਨੀ ਚਾਹੀਦੀ ਹੈ।
ਪ੍ਰਦੂਸ਼ਣ ਪ੍ਰਤੀਰੋਧ:ਸੋਲਡਰਮਾਸਕ ਨੂੰ ਦੂਸ਼ਿਤ ਤੱਤਾਂ ਤੋਂ ਵੀ ਬਚਾਉਣਾ ਚਾਹੀਦਾ ਹੈ ਜੋ ਪੀਸੀਬੀ ਦੀ ਕਾਰਗੁਜ਼ਾਰੀ ਨੂੰ ਪ੍ਰਭਾਵਤ ਕਰ ਸਕਦੇ ਹਨ। ਇਹ ਉਹਨਾਂ ਐਪਲੀਕੇਸ਼ਨਾਂ ਵਿੱਚ ਖਾਸ ਤੌਰ 'ਤੇ ਮਹੱਤਵਪੂਰਨ ਹੈ ਜਿੱਥੇ PCB ਨੂੰ ਧੂੜ, ਰਸਾਇਣਾਂ, ਜਾਂ ਹੋਰ ਪ੍ਰਦੂਸ਼ਕਾਂ ਦੇ ਸੰਪਰਕ ਵਿੱਚ ਆ ਸਕਦਾ ਹੈ।
ਪੀਸੀਬੀ ਨਿਰਮਾਣ ਪ੍ਰਕਿਰਿਆ ਦੇ ਨਾਲ ਅਨੁਕੂਲਤਾ
ਸਹੀ ਸੋਲਡਰਮਾਸਕ ਦੀ ਚੋਣ ਕਰਨ ਵਿੱਚ ਇੱਕ ਹੋਰ ਮਹੱਤਵਪੂਰਨ ਕਾਰਕ ਪੀਸੀਬੀ ਨਿਰਮਾਣ ਪ੍ਰਕਿਰਿਆ ਦੇ ਨਾਲ ਇਸਦੀ ਅਨੁਕੂਲਤਾ ਹੈ। ਸਖ਼ਤ-ਫਲੈਕਸ ਪੀਸੀਬੀ ਵੱਖ-ਵੱਖ ਨਿਰਮਾਣ ਕਦਮਾਂ ਵਿੱਚੋਂ ਗੁਜ਼ਰਦੇ ਹਨ, ਜਿਸ ਵਿੱਚ ਲੈਮੀਨੇਸ਼ਨ, ਐਚਿੰਗ ਅਤੇ ਸੋਲਡਰਿੰਗ ਸ਼ਾਮਲ ਹਨ। ਸੋਲਡਰਮਾਸਕ ਆਪਣੀਆਂ ਸੁਰੱਖਿਆ ਵਿਸ਼ੇਸ਼ਤਾਵਾਂ ਨੂੰ ਘਟਾਏ ਜਾਂ ਗੁਆਏ ਬਿਨਾਂ ਇਹਨਾਂ ਪ੍ਰਕਿਰਿਆਵਾਂ ਦਾ ਸਾਮ੍ਹਣਾ ਕਰਨ ਦੇ ਯੋਗ ਹੋਣਾ ਚਾਹੀਦਾ ਹੈ।
ਲੈਮੀਨੇਸ਼ਨ:ਸੋਲਡਰਮਾਸਕ ਸਖ਼ਤ ਅਤੇ ਲਚਕਦਾਰ ਪਰਤਾਂ ਨੂੰ ਬੰਨ੍ਹਣ ਲਈ ਵਰਤੀ ਜਾਂਦੀ ਲੈਮੀਨੇਸ਼ਨ ਪ੍ਰਕਿਰਿਆ ਦੇ ਅਨੁਕੂਲ ਹੋਣਾ ਚਾਹੀਦਾ ਹੈ। ਇਸ ਨਾਜ਼ੁਕ ਕਦਮ ਦੇ ਦੌਰਾਨ ਇਸ ਨੂੰ ਡੀਲਾਮੀਨੇਟ ਜਾਂ ਦੂਰ ਨਹੀਂ ਕਰਨਾ ਚਾਹੀਦਾ ਹੈ।
ਐਚਿੰਗ:ਸੋਲਡਰਮਾਸਕ ਸਰਕਟ ਪੈਟਰਨ ਬਣਾਉਣ ਲਈ ਵਰਤੀ ਜਾਂਦੀ ਐਚਿੰਗ ਪ੍ਰਕਿਰਿਆ ਦਾ ਸਾਮ੍ਹਣਾ ਕਰਨ ਦੇ ਯੋਗ ਹੋਣਾ ਚਾਹੀਦਾ ਹੈ। ਇਸ ਨੂੰ ਸਟੀਕ ਐਚਿੰਗ ਦੀ ਆਗਿਆ ਦਿੰਦੇ ਹੋਏ ਅੰਡਰਲਾਈੰਗ ਤਾਂਬੇ ਦੇ ਨਿਸ਼ਾਨਾਂ ਨੂੰ ਲੋੜੀਂਦੀ ਸੁਰੱਖਿਆ ਪ੍ਰਦਾਨ ਕਰਨੀ ਚਾਹੀਦੀ ਹੈ।
ਸੋਲਡਰਿੰਗ:ਸੋਲਡਰਮਾਸਕ ਪਿਘਲਣ ਜਾਂ ਵਿਗਾੜਨ ਤੋਂ ਬਿਨਾਂ ਸੋਲਡਰਿੰਗ ਨਾਲ ਜੁੜੇ ਉੱਚ ਤਾਪਮਾਨਾਂ ਨੂੰ ਸਹਿਣ ਦੇ ਯੋਗ ਹੋਣਾ ਚਾਹੀਦਾ ਹੈ। ਇਹ ਲਚਕੀਲੇ ਭਾਗਾਂ ਲਈ ਵਿਸ਼ੇਸ਼ ਤੌਰ 'ਤੇ ਮਹੱਤਵਪੂਰਨ ਹੈ, ਜੋ ਗਰਮੀ ਦੇ ਨੁਕਸਾਨ ਲਈ ਵਧੇਰੇ ਸੰਵੇਦਨਸ਼ੀਲ ਹੋ ਸਕਦੇ ਹਨ।
ਸਖ਼ਤ-ਫਲੈਕਸ ਪੀਸੀਬੀ ਸਮਰੱਥਾ
Rigid-Flex PCBs ਦੀਆਂ ਸਮਰੱਥਾਵਾਂ ਸਿਰਫ਼ ਉਹਨਾਂ ਦੀ ਭੌਤਿਕ ਬਣਤਰ ਤੋਂ ਪਰੇ ਹਨ। ਉਹ ਗੁੰਝਲਦਾਰ ਰੂਟਿੰਗ ਅਤੇ ਕੰਪੋਨੈਂਟ ਪਲੇਸਮੈਂਟ ਲਈ ਕਈ ਲੇਅਰਾਂ ਦੇ ਨਾਲ ਗੁੰਝਲਦਾਰ ਡਿਜ਼ਾਈਨ ਦਾ ਸਮਰਥਨ ਕਰ ਸਕਦੇ ਹਨ। ਸੋਲਡਰਮਾਸਕ ਦੀ ਚੋਣ ਕਰਦੇ ਸਮੇਂ, ਇਹ ਵਿਚਾਰ ਕਰਨਾ ਜ਼ਰੂਰੀ ਹੈ ਕਿ ਇਹ ਇਹਨਾਂ ਸਮਰੱਥਾਵਾਂ ਨਾਲ ਕਿਵੇਂ ਪਰਸਪਰ ਪ੍ਰਭਾਵ ਪਾਵੇਗਾ। ਸੋਲਡਰਮਾਸਕ ਨੂੰ ਪੀਸੀਬੀ ਦੀ ਕਾਰਗੁਜ਼ਾਰੀ ਵਿੱਚ ਰੁਕਾਵਟ ਨਹੀਂ ਪਾਉਣੀ ਚਾਹੀਦੀ, ਸਗੋਂ ਇਸਦੀ ਕਾਰਜਸ਼ੀਲਤਾ ਨੂੰ ਵਧਾਉਣਾ ਚਾਹੀਦਾ ਹੈ।
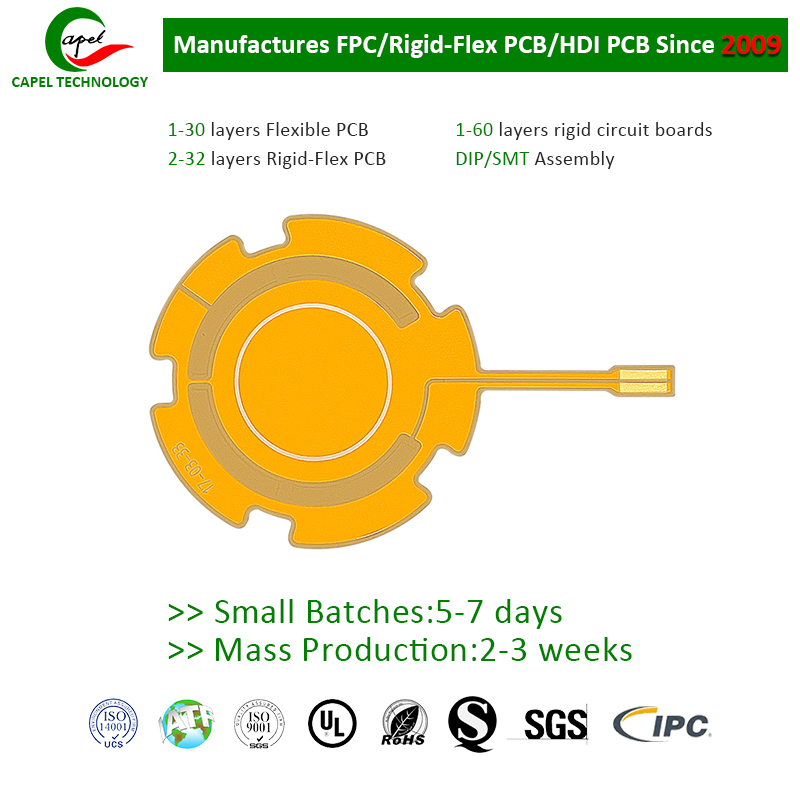
ਪੋਸਟ ਟਾਈਮ: ਨਵੰਬਰ-08-2024
ਪਿੱਛੇ